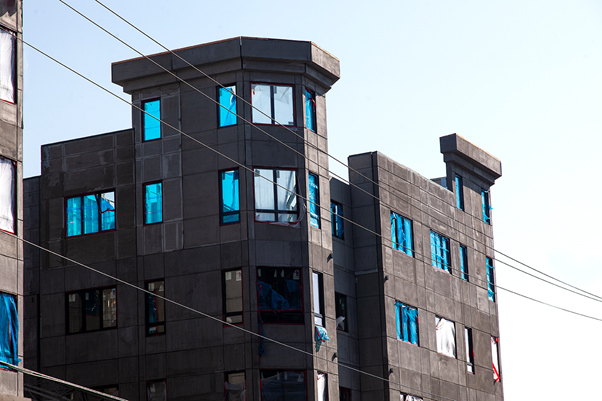
Claiming a piece of land is always an overwhelming experience, and sometimes there could be things that we overlook when doing so. But now there are a variety of construction options that you can choose from, and it becomes difficult to make the right choice. The most common are traditional constructions and pre-engineered steel buildings. If you are thinking of buying a modular structure, then here are a few things you should read.
What Are Modular Buildings?
In simple words, modular buildings are pre-engineered steel buildings. These include pre-manufactured modules that are fabricated in factories. These are built with standard building materials and constructed using assembly-line methods.
There are different types of pre-engineered steel buildings such as modular, panelized, and pre-cut buildings. The structure is also selected on the basis of the location and materials. Modular structures are built in two to three modules only with the interior fittings to leave only a little finishing after the assembly, while panelized buildings are built in panels or walls of the building as a whole. Pre-cut structures are built as an entire assembling kit, with the various modules of a wall to the smallest interior fittings. As the name suggests, everything is pre-cut to later fit like a jigsaw puzzle.
What Are the Pros and Cons of Modular Buildings?
Pre-engineered steel buildings are incredibly beneficial as they are less expensive than traditional construction. Along with paying less, you can also claim the modular structure to be yours in less time as compared to a conventional construction. The design and size are customizable according to your preferences. You must have thought that flexible aesthetics is possible only in traditionally-built structures, but modular structures also allow design flexibility. These pre-engineered steel buildings are built using eco-friendly materials and steel frames, which do not cost much and are incredibly energy-efficient. The materials used, the method and airtight construction produce an energy-efficient space that will reduce your utility bills.
No matter how flexible the modular structures are, there a few downsides. Although you can customize according to your liking, there will be a few limitations to selecting a few interior designs. You would still have a variety of other options to choose from for your modular structure.
What Are the Steps to Buying Modular Buildings?
Property: When selecting a piece of land, you must be able to identify the grade and soil compaction. The grade refers to the slope of the landform while soil compaction is the ability of the soil to stress itself into densifying and displacing the air outside. You may also have to consider the various factors of water, sewer, facilities and existing buildings. Moreover, you need to understand the local governing body and municipality where you will be staying. To ensure how easy-going or harsh they are because you will be going through a permitting process and periodic inspections where you will be required to interact with them. You need to look at a lot of aspects to select the right location for your modular building.
Design: Usually, for traditional structures, you would contact an architect who would have several construction builders in association with them. Nowadays, you can have your project owners contact a modular construction company having the skills to perform a complete design and build procedure. Either way, you can expect a high-quality pre-engineered steel building and have the freedom to select the designs you like for interiors and exteriors. While meeting the state and federal regulations for the design and structure is left in the hands of the construction company.
Proposal: You get to see the design and tiny details so that you can approve before the company starts building your pre-engineered steel building. The formal plan includes delegation of tasks, pricing, schedule, sketches and specifications of the structure.
Approval: In most cases, the permit can be issued by the customer while the modular construction company secures it with an additional fee. The authorization is the only step that could hold you back depending on where your property is because you need approval by the local authorities.
Contract: The contract form varies depending on the size and design of your pre-engineered steel building. Mostly, the modular structures are billed based on the periodic percentage of project completion or milestone achievements.
Preparation: Before your pre-engineered steel building is assembled, site preparation will be required. The site preparation will be carried out by the modular construction crew and will include surveying, excavation, demolition, foundation work and utility installation.
Fabrication: The finalized structure design is sent to the modular construction factory where they will execute the plan. The modules constructed in an assembly-line method will have the support structure, electrical, plumbing, mechanical, insulation, door, window, exterior and interior modules built in the factory.
Installation: The modules of the entire structure is delivered to the site for installation once it is constructed. The modular sections are carefully placed on the foundation one at a time. The walls, ceilings, plumbing, and electrical systems are installed according to the fabrication design. The connections are made at every mate line, which is the point where the modules or sections meet. After all the interior modules are installed, the exterior modules are finished up by connecting with water, sewer, data lines, and utilities. In the end, the other work is completed, such as the site restoration, paving, and landscaping.
Occupancy: You will receive a certificate of occupancy after all the inspections and approval of the local authorities on completion.
Now you have your own modular structure ready to occupy and own. If you maintain the modular structure properly, these pre-engineered steel buildings will last up to twenty to thirty years. To have your customized modular structure, contact a reputed construction company.