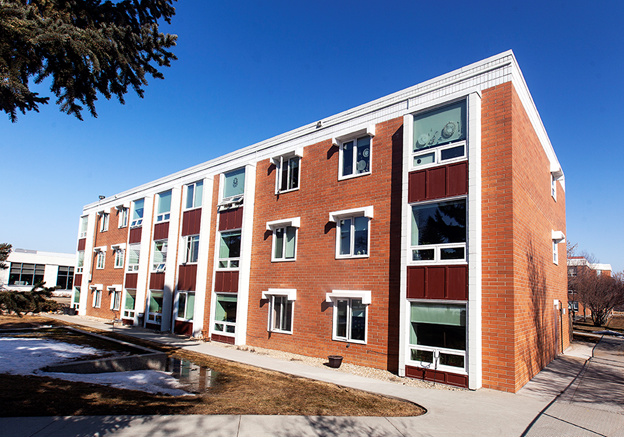
Construction projects are vast processes that take place for a long time. The procedure involves the use of raw materials in bulk quantities and the help of several labourers. Throughout the process, the people working on site and also the people around the site have to numerous challenges. Most of these challenges are known to be overcome by modular construction technique. We already know that modular construction is better than the traditional method in various ways. Let us look at some of those challenges that modular construction makes easier.
1) Delays Due to Natural Factors
The first challenge that modular construction overcomes is the potential delays caused due to extreme weather. When the temperature dips or when it rains heavily, the traditional construction process gets affected. The project has to be paused until the climatic conditions get back to normal. Also, the raw materials are also affected, especially when it rains or snows. Apart from the climate, other natural factors such as natural calamities and fire outbreak also affect the project. The modular construction process involves in-factory prefabrication of units or modules of the building. This step takes up the majority of the time. As the procedure is done in an enclosed and safe setting, the modules and their integrity aren’t affected. Also, modular fabricators can wait for the situation around the desired site to be ideal before installing all the modules together on the site. This way, there are absolutely no delays in the procedure due to any external factors.
2) Difficult Construction at Remote Locations
Traditional construction involves the transportation of raw materials and machines daily. Also, a lot of labourers need to access the site daily. Both of these can become too hectic if you are planning to build a structure in a remote location. Accessing and transporting heavy equipment through a narrow and limited passage regularly is difficult. Hence, the duration of construction projects at hard-to-reach places is often extended. But there aren’t any delays or much difficulty when you erect a building by the modular technique. As the major part of modular structure construction takes place off-site, in a factory setting, the need to access the remote location daily is reduced. The only time workers access the remote location is during the final assembly stage.
3) Disturbance to Neighbouring Life
We all have seen how invasive traditional construction projects are. When a new building is being erected, it takes up an entire area. Nobody can access the area for months. And if the building is being constructed at a central location that connects two roads, the connection is disturbed, and people have to alter their lifestyle. Plus, the construction process creates a lot of noise and air pollution. Big machines used in the process make noise and the loose mud particles contribute to pollution. This is where modular construction is a less invasive alternative. As the major part of the entire procedure takes place inside closed factories, nobody outside is disturbed. Also, the onsite assembly doesn’t create much noise or any kind of pollution. Plus, as the process takes place quickly, the location isn’t shut for a long time. In simpler words, nobody is affected when a modular construction project is in process.
4) Additions to an Existing Structure
One of the major benefits of modular construction is that it allows you to add additional wings to an existing structure. Suppose if you have a hospital and you wish to add a few wards or just an additional wing to it, it can be difficult with traditional construction. Modular construction, on the other hand, can make this thing happen easily. The additional units of the new structure are fabricated in factories and then they are attached to the existing structure. This existing structure can be either a modular building or even a traditionally-built one. This construction technique makes it happen. And not only that, the process is not at all hectic and time-consuming. It only takes about a few weeks.
5) Long-lasting Construction Processes
The traditional construction process takes a very long time. Right from site preparation to erecting a building to finishing it with paints and other necessary things, the entire project is time-consuming and vast. But when you talk about modular construction, the process gets done within 1/4th time compared to the traditional construction project of the same extent. The process of in-factory prefabrication and on-site assembly happens within a matter of a few weeks, unlike the traditional construction where it takes several months. So if there’s an urgent requirement for building a structure and occupying it soon, modular construction can be the right technique to follow.
6) Poor Quality of Structure
A lot of constructors often buy cheap raw materials such as cement, stones, bricks, etc. just to save a few dollars. But the outcome of any construction using such materials is poor. Buildings made using low-quality and cheap raw materials collapse at any point or get structural damage much earlier than they actually should. People then have to invest a lot of additional money and time to repair the flaws that can compromise the overall quality of the structure. Structural damage isn’t an issue with modular construction, and there are several reasons for this. Firstly, the raw materials used in this process are high-quality metal, mostly structural steel, and wood. These materials are environment-friendly, and a lot of them are also recycled from other construction processes. Secondly, all the modular construction buildings meet the requirements of quality. This means that there aren’t any chances of issues.
Apart from these, manpower is also a challenge that modular construction overcomes. You need a lot of people to complete different types of tasks involved in traditional construction. But when you hire modular construction experts, you will only require a team of specialists who will ensure the completion of your project with precision and in time.