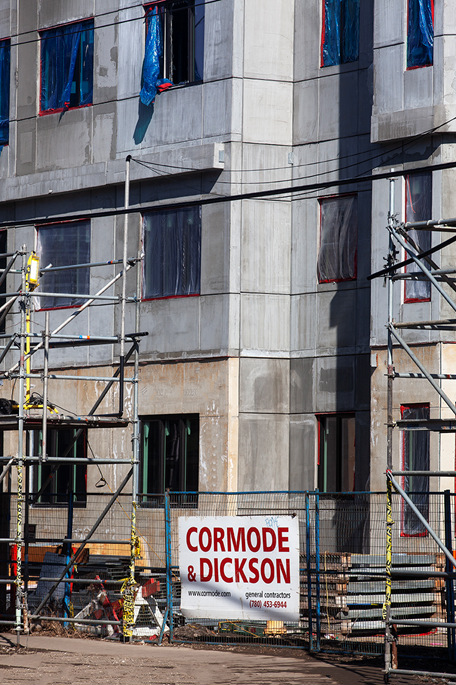
If this is your first time of building a modular structure for your commercial use, then you may end up missing out on some crucial steps or making mistakes. To avoid anything from going wrong, here’s a complete checklist that you must keep handy.
1) Find the Land
Firstly, you will have to find the right piece of land to erect a modular building. Find a place that isn’t very remote as you don’t want people to face a hard time commuting to and reaching your location. Once you find the right land with enough square footage, determine how you will finance to buy that land. If you are planning to erect a permanent modular building, leasing or renting a piece of land isn’t an option for you.
2) Hire a Modular Building Dealer
Once you have the land ready, you must then look for a modular building dealer. This professional will work with you to plan, design, and build the modular structure that suits your expectations. Look at the years of experience, types of services, past clients, construction approach, reputation, and pricing structure of various modular construction specialists. Compare several options, talk to each one of them, and only then hire the right dealer.
3) Communication and Inspection
Once you find the right modular dealer, talk to them and explain why you wish to erect a modular building. Explain your purpose, expectations, budgets, timelines, and everything else about the modular project. The dealer will then get back with you with their rough plan of how you can go about the entire project. They will also let you know if your expectations will be practical to follow and fit within the budget.
4) Get the Necessary Permits
You’ll need to review your building plans with your city and acquire the necessary permits before you can begin working on the construction site. Some of the permits that you need include:
- Land Survey
- Land Use Compliance Certificate
- Zoning Exception
- Site Plan Approval
- Environmental Permits
- Commercial Building Permit
- Water Approval
- Electric Approval
- Sanitation Approval
Once your plans are approved, you can get started.
5) Project Planning and Designing
Now is the time when the entire modular construction team and your team will have to sit together and move ahead with the actual plan of the building. A blueprint and dummy model will be prepared in this stage so that everybody gets an idea of what the final modular building will look like and how will people go about the construction process.
6) Advance Payment
You will have to make the advance payment to the dealer as the token of surety. Once you make the payment, the process will then commence.
7) Ground Preparation
This is the most important step of the process. If the land isn’t prepared and levelled, it can pose dangers to the modular building in the future. Steps in ground preparation of site involve site clearing, excavation, grading and compaction.
8) Foundation Laying
When the land is completely ready after clearing the land, loosening the soil, and creating the right slopes, the foundation laying work will start. Surveyors set stakes on-site. Excavators dig the foundation hole. The foundation is installed.
This is the time when the fabrication process of modules will also go on simultaneously in factories. The benefit of modular construction is that the site work and plant work can happen side-by-side which dramatically decreases your overall timeline.
9) Fabrication of Modules
As per the design that was created by the modular construction team, the modules or pieces of the modular building are fabricated in controlled factory settings. When all of this construction is complete, the manufacturer wraps the modules and ships them to the building site to be assembled.
10) Modular Building’s Delivery and Assembly
Once both the modules and the site are ready, the modules will be delivered on the desired site. These modules will then be placed together carefully. Just like any jigsaw puzzle tower, the entire modular building will be erected on the foundation and clear land. The assembly process generally takes 2-3 days.
11) Air Sealing
When the modules are placed side by side or stacked on top of each other, significant gaps are created. It is essential to get rid of these gaps to ensure energy efficiency of the modular building. Hence, your modular construction dealer will air seal the building before any finishing touches.
12) Modular Additions
Depending on your preferences, the additional amenities will then be constructed or added to the modular building. Staircase, garages, doors, windows, plumbing system, and other amenities and features will be added to the structure once the building is erected.
13) Painting and Beautification
As like any other traditionally-built building, even the modular building will be beautified by painting and decorating. If you opted for a lawn area around the building, the right people will get to work and carry out complete landscaping for you.
14) Site Clearing
Every construction project results in a lot of mess and waste products. This mess will be created by the team of your modular construction dealer. You don’t have to worry about this as the construction team will leave your premises only after making it fully ready for occupying and using.
15) Full Payment
The rest of the payment for the entire project will have to be made after the project is over. The project will ideally get completed here.
When you hire a reputed and experienced team of modular experts, this entire process of modular building construction will go on smoothly. You won’t have to worry about the quality and efficiency of your building. So why wait? Hire Cormode & Dickson for your modular building needs as we provide nothing but incomparable modular construction services.