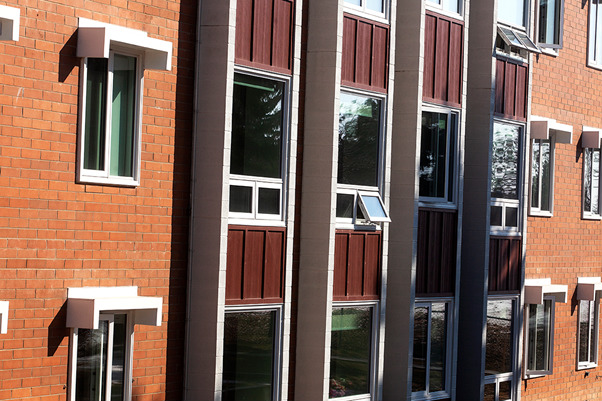
If you are soon going to start a new construction project for your commercial use, you must know that modular construction can be one of your choices. The process of modular construction is very different and a lot better than the traditional construction. To understand the concept of modular construction better, you must know the steps involved in the process.
Property Identification
The site selected for the modular construction is very important because it will have a direct impact on many other components of the process. The soil compaction, grade or slope of the land, water, sewer, utilities, and existing structures in the vicinity are all taken into consideration when choosing the right property for erecting a modular structure.
Proposal Outlining
The formal proposal allows you and your modular fabricator to see everything together before executing a contract. A typical proposal may include:
- Assignment of various responsibilities and tasks
- Pricing
- Project schedule
- Different terms
- Clarifications
- Exclusions (so that you know what is not being included)
- Floor plan and building specifications
Project Planning
This phase creates a description of the modular structure, usually represented by detailed plans and specifications. Some of the building parameter questions that your modular fabricator may ask you include:
- What is the project budget?
- Has land been acquired?
- Is the building intended for temporary or permanent occupation?
- How soon will the building be occupied?
- How many people will the structure house?
- How much square footage is required?
- How many modules will be required?
- How many bathrooms are required?
- Are fire suppression systems required?
- What direction will the building face?
- What exterior finish do you want?
- What interior finish do you want?
- What flooring do you want?
- What kind of foundation is appropriate?
Once you and your fabricator get answers to these questions, they can take the next steps then.
Designing
Once you answer these questions, the fabricator will work with you to create the basic design plan of the modular structure. If you need any alterations in the design, you can ask for them at this stage itself. The use of building information modelling (BIM) will allow you to see what the finished product will look like before manufacturing begins. The added advantage of this approach is that the final cost should not differ from the initial quote, helping you to plan and control your overall expenditure.
Getting Permits
In most cases permits are obtained by the customer but can be secured by the modular dealer, typically for an additional fee. It is important to find out what the local officials require as early in the overall process as possible because the actual approval of the permit application can take significant time. Typical construction permits required can include:
- Site plan
- Building permit
- Mechanical permit
- Plumbing permit
- Concrete permit
- Encroachment permit
- Sign permit
- Flood district development permit
Module Manufacturing
The individual sections or modules of the structure are built in a factory-controlled setting where the basic structure or the skeleton of the structure start coming together. By doing this in a factory setting, the fabricators ensure that the process is done efficiently and with less material waste than traditional stick-built construction.
Site Preparing and Foundation Laying
As the modules are fabricated in the factory, the site preparation work is simultaneously done on the property. Two separate crews are in constant communication and collaboration with one another to ensure that the same timeline is being followed and milestones will be met at the same time. This is the reason why modular construction is considered to be a fast process compared to the traditional construction technique.
Delivering the Modules
Once the modules are fabricated and property is fully ready too, the modules will be transported to the site. This will take the usual time of transport from the factory to your desired site. These modules will be transported using special tow trucks.
Assembling
Once all the modules are transported, they will be assembled and installed together. The custom modular units are meticulously placed on the foundation one at a time, next to each other, so they line up exactly. Just like Lego pieces, these modules will be assembled together to complete the modular structure. During this process, the walls, ceilings, electrical, data, plumbing, and HVAC systems are all installed so that they line up correctly with the modules on either side.
Final Finishing
The final step in the process is connecting the utilities. Exterior cladding (which starts in the factory) is finished off on-site, as is plastering and painting. This step is all about the details. Interior work begins, such as painting and furniture delivery. As this happens, exterior work and landscaping are being done as well. This is the phase in which your modular building will be completed and truly become something habitable.
Project Completion
Your modular building is complete! Both the keys and the ownership will be transferred to you at this point, and it’s time for you to get use out of your new modular structure.
Custom modular buildings are built to meet all applicable state and local codes and can be tailored to meet the highest energy standards you desire. This means that you don’t have to worry about the code compliance of the final modular structure.
So now that you know the entire process of this construction method, you can consider modular construction for your next project. When looking for a reliable modular construction specialist, think about hiring Canada’s leading commercial construction contractor – Cormode and Dickson