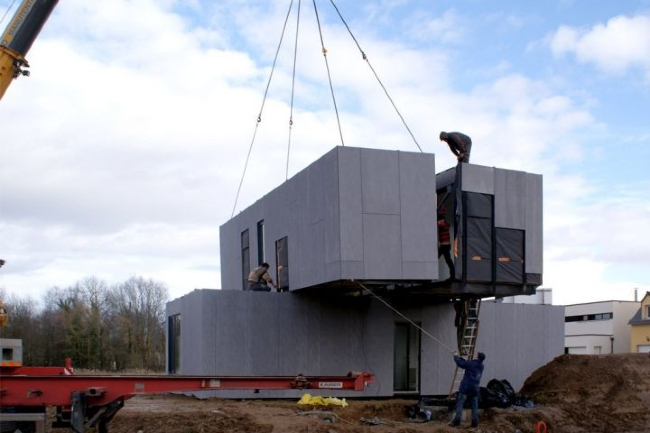
Quality assurance is one of the most vital aspects in almost every industry. And, when it comes to construction, it is ‘the’ most vital aspect. With architects increasingly looking for perfection in construction, modular buildings are providing them with just that, and more. Unlike conventional construction methods, modular construction is carried out with more measures taken into consideration. Modular construction is considered a boon because of its stringent quality checks at every stage and much more restrictions in the construction, overall. All this takes place to ensure that the end product will be outstanding without compromising on quality.
Do you wish to delve deeper into how exactly do modular buildings enhance construction quality control? Read on to know the exact technicalities of the process.
Inspection and Storage of Materials
In conventional construction methods, raw materials are brought and later stored on the construction site. This leads in them getting exposed to climate and weather fluctuations. This lack of care in the initial stages can damage the construction in the long run. However, when it comes to modular construction, the dry raw materials are manufactured and stored in a safe and dry place. The raw materials undergo a proper inspection and are given the necessary approval. This keeps the materials away from the elements like air, water or snow.
Construction Quality Control on Site
Even though the materials undergo a proper procedure, construction quality control on-site is still important so it doesn’t affect the construction in the long run. To enhance construction quality control of modular buildings, proper verification of local, government and state laws and regulations are done. The manufacturers of modular buildings follow stringent procedures with formal quality programs in every stage. The programs ensure if it can withstand the pressures of travelling and transportation.
Efficiency Due to Planning
In conventional construction, planning can sometimes be a barrier because of the availability of raw materials or other factors. However, when it comes to modular buildings, construction quality control solidifies because the materials are already available, tested and inspected. This makes it easier for architects, planners and consultants to efficiently plan further. All the planning is done collaboratively which enhances the construction quality control. Since the teams work together to carry out planning and execution simultaneously, the work gets done faster. Thus, time delays and construction mishandlings are a rare sight.
Effective Coordination
Modular construction is a success in these modern times because of successful coordination. Coordination between design teams, architects, site managers, construction specialists, etc. brings together people from different teams to a central discussion. All the teams properly coordinate, plan their future actions, sketch out a design and finally implement it after final agreement. Effective coordination is thus important so imbalanced decisions don’t affect the construction in the long run.
With the commendable features of portability and storage efficiency of construction elements, builders and architects are greatly looking forward to modular buildings. And to take advantage of the same benefits with great assistance in modular construction, you can always talk to our specialist at Cormode and Dickson.