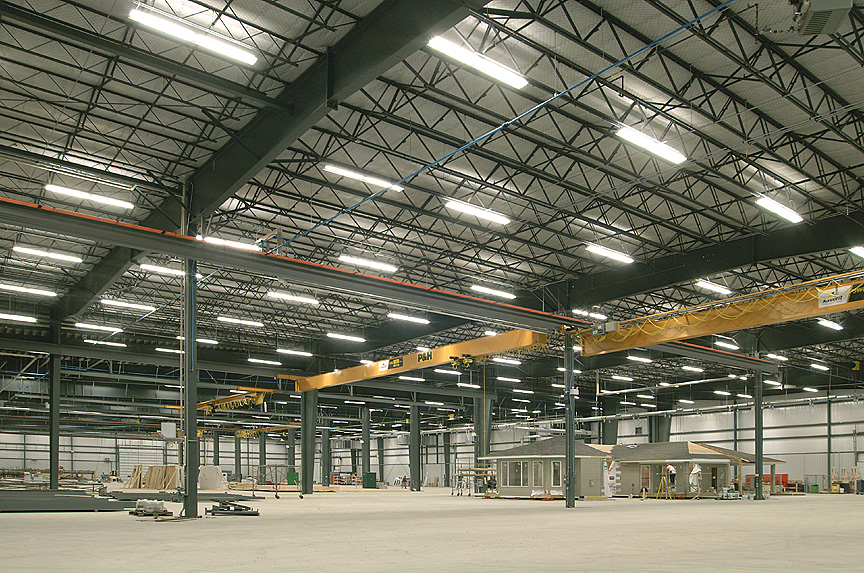
The first ever recorded modular building appeared in the South Australian Record in 1837. The structure was designed and built by carpenter Henry Manning, who built the components in London and shipped them to Australia, for a ready-made portable cottage. That puts modular buildings at almost 200 years old. So, why are there so many myths and misconceptions surrounding modular buildings?
It’s still a relatively new form of building to most project managers, architects, and construction workers, even if it’s been around for quite some time. That’s why we wanted to dispel some of the misconceptions surrounding the buildings.
Myth 1: Modular construction can’t be built more than 4 levels.
At Cormode & Dickson, most of our modular projects have been in the four levels or below range, but we have plans to build 5-6 level structures using modular technology in the very near future. In Vancouver, there was recently a green light by modular company Atira to build a 7 level modular building. You can read about that here.
We also recently wrote a blog about how the construction industry has overcome their perceived limitations, by building modular wood buildings over 4 levels, and changing the building codes to reflect that. You can read about that here.
Myth 2: Modular construction is more expensive than conventional construction.
Modular construction is sometimes seen as a new or different technology, and as a result, some may believe that it is more expensive than conventional or traditional stick built construction.
However, when you consider the expedited schedule time, modular is the much cheaper option. You spend less money on labour, less money on loan interest, there is much less material waste, and you start receiving income 30 to 50% sooner than traditional construction.
Myth 3: Modular construction all looks the same.
One of our most recent projects, the North Ridge Place, built in St. Albert, proved that all our projects don’t look the same. This project was a 47, 520 sq. ft., 48 suite addition to the already existing North Ridge Lodge, a seniors’ assisted living housing development managed by the Sturgeon Foundation. The perfect example of the flexibility of modular, this addition was built off site, then delivered, which dramatically expedited the schedule and allowed for completion of the facility within a much shorter time frame. The exterior siding was a maintenance free product that served to ‘mask’ the modular construction, and seamlessly integrate itself into the already existing structure.
Myth 4: Modular construction has poorer quality standards and sub-standard insulation.
With the materials built in a weather-controlled factory, they have little to no on-site damages, and are always built to the highest standards. Plus, fabrication facilities have notoriously high QA/QC standards, with regular, independent inspection and testing protocols.
Myth 5: Modular construction are always temporary.
Depending on the type of building you want to produce, you can choose between either Permanent Modular Construction (PMC) buildings or Relocatable Buildings (RBs). Like most things in modular, it can be built to the exact specifications, requirements, and desires that you wish to build it.