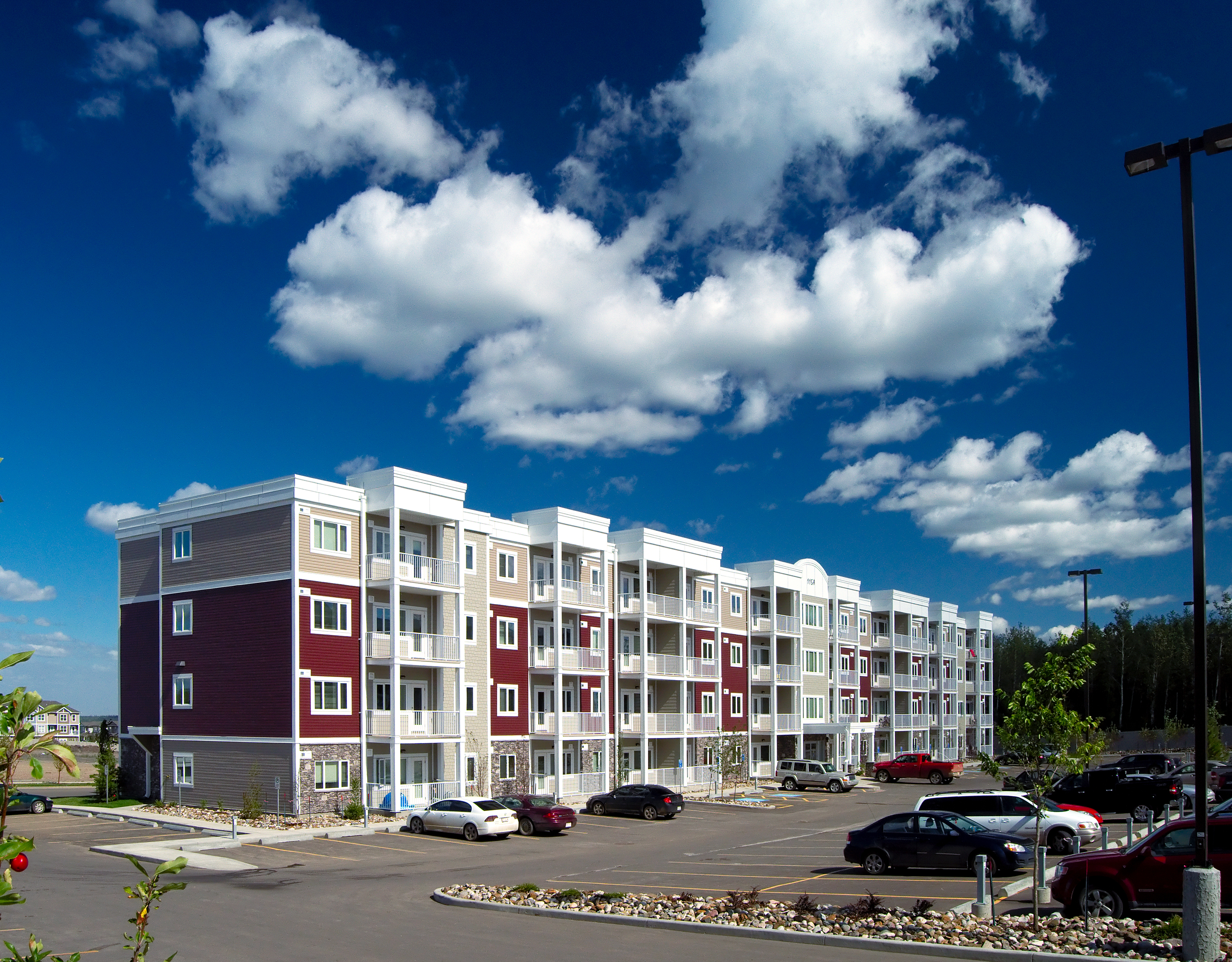
Is there a schedule advantage for modular? To put it simply, yes there is, but let’s find out more.
When you consider the advantages of modular construction, you’ll find time and time again, the number one advantage that comes up is the expedited build schedule. General estimates have modular construction cutting the building schedule of a project by at least 30 to 50%, when compared to conventional construction. That means increased revenue for your construction project and 30 to 50% less spent on construction costs.
But why is there an expedited schedule? There’s a number of reasons.
“A recent report by the National Institute of Standards and Technology and the National Research Council identifies modular construction as an under-utilized resource and a breakthrough for the U.S. construction industry to advance its competitiveness and efficiency.”
First, the construction is simultaneously done with site work, allowing projects to be completed in half the time of traditional construction, allowing a builder to have modules on-site and ready right as the foundation has completed and the concrete has cured.
The elimination of weather delays, because of factory-built conditions. 60-90% of the construction is completed inside a factory setting, which almost completely mitigates the risk of weather delays.
For example, we were tasked with the modular installation of the Noralta Lodge Camps in Fort McMurray, Alberta, and they had this to say: “Timeline and budget were met, thanks to the exceptional Cormode delivery team and their undeniable commitment to excellence.”
Experts in the field expect the relocatable modular building industry to grow faster than the market in general due the growing use of BIM, owners wanting projects faster and for lower cost, safety, quality and the shortage of skilled labor once markets return to more normal growth.