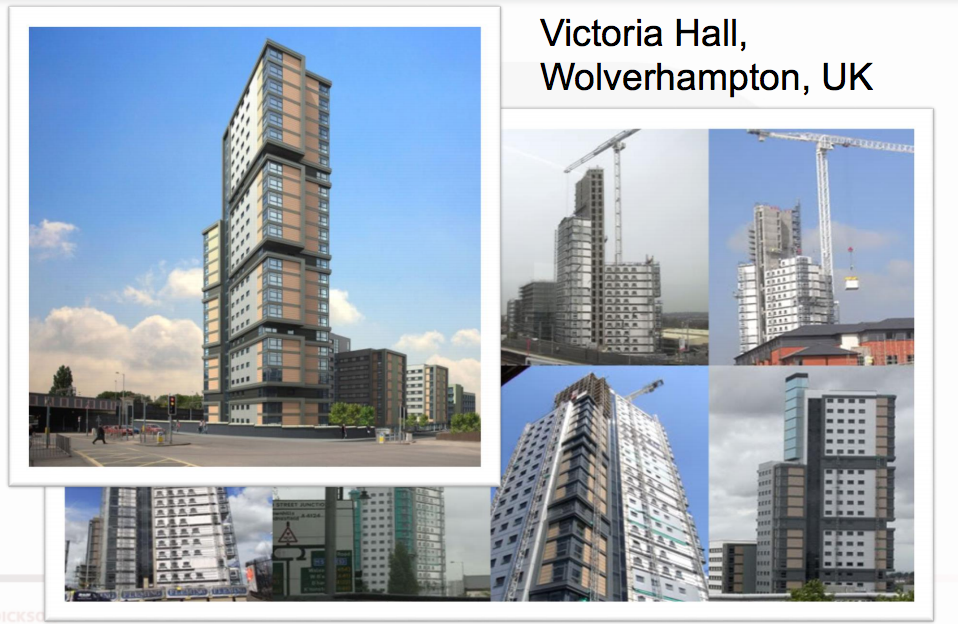
About two weeks ago, our very own Randy Ludwar, VP of Operations, attended the longest running, largest modular event of the year: 2016’s 33rd Annual World Of Modular in San Diego, California. The event was a massive success, for both the industry, and for Cormode & Dickson.
Here’s a brief recap, in case you missed it:
What you may or may not already know, is that Randy Ludwar presented a well-received presentation on “Modular By The Numbers.”
In today’s blog, for those who unfortunately couldn’t attend, we wanted to go through the presentation.
Here it is:
In 2012, there were 977 workplace deaths recorded in Canada, an increase from 919 the previous year, representing more than 2.7 deaths a day. The eventual goal is, of course, to make that number a zero. What’s a significant way to decrease that number? Well, it’s no surprise, but off-site modular construction improves BOTH the quality and the safety of projects.
“Safety is perhaps the most important benefit of off-site manufacturing,” says Mark Konchar, senior vice president of Enterprise Development for Balfour. Not only are employees working in a safe environment, with less risk of injury, but safety on the jobsite is improved. “We are looking closely at the impacts on safety such as less trades working on-site and how we eliminate risk,” he says.
“Safety is paramount, budget and schedule are soon forgotten but quality and safety will be visible and documented forever.” — Randy Ludwar
The perception of modular construction from 10 years ago included ‘trailers,’ portables,’ cheap, poor quality, cramped and dingy, uncomfortable, unhealthy, and short lifespan. But it’s come a long, long way!
At a glance, what are the quick advantages of modular construction?
- Centralized control, lean manufacturing
- Factory operatives, due to repetitive familiarity, breed regularity and decrease labour inputs by as much as 30%
- Shorter onsite construction schedules, from 30% to 50%.
- An unmatched level of quality control, due to factory-controlled conditions.
- Better ROI
- Lower employee travel and living costs
- Safety is significantly improved
- Less waste: waste could be as low as 1.5% while traditional on-site construction is up to 10%.
- Workers can be older and can work longer, due to less physical impact and increased automation.
How fast is the construction industry catching on? A McGraw Hill White Paper estimates that 98% of all projects is doing some prefabrication.
Who is the ideal client for a modular project?
- Clients who are open to change and believe in outside-the-box thinking.
- The design is 100% complete prior to project initiation, so that it is built to modular specifications.
- Project managers who don’t believe in “the way they’ve always done it.”
- High front-end cash flow.
- Clients who believe in high QA/QC and higher safety controls.
- Note: ALL projects can be built to modular. We’re highly adaptable. Get a free consultation to the right of your screen!
The future of modular: “46% less carbon foot print with offsite modular in comparison to site built” due to lower onsite travel, material delivery, weather conditions.” Dr Mohamed Al-Hussen, PhD, P.Eng., Professor, Engineering Faculty U of A.
When does Cormode & Dickson come into a project? At the beginning. A design-bid-build process does not work in this environment.
Project highlight showing the capabilities of Modular: Victoria Hall, Wolverhampton, UK.
World’s tallest modular structure with 24 prefabricated, modularly built floors out 25 total floors. This student residency, built by Vision Modular Solutions, was completed in 2009. Modules constructed of 60 x 60 HSS @ 600 oc bearing sidewalls with poured concrete floors and were cantilevered portions supported by structural steel ‘H’ Frames on exterior modules.
For more examples of surprising projects that were built modular, sign up and download Randy Ludwar’s full presentation here!