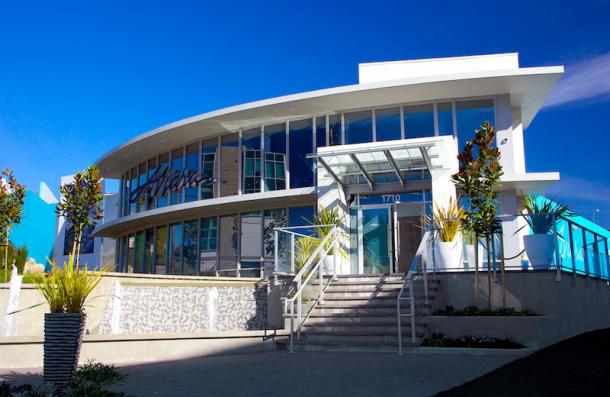
Ben Webster at EarthTechling notes that traditional home builds (for a 2,000 sq.ft. home) result in over 8,000 pounds of landfill waste. Additionally, as noted in our post on The Resource Efficiency of Modular Construction, a new, traditionally constructed commercial or industrial building generates about 3.9lbs of waste per square foot. And while green initiatives like waste recycling offset these environmental impacts, modular construction facilities the transfer of leftover materials from one project to the next, reducing waste through inventory control and protecting building materials. Prefabrication also reduces transportation waste, since workers are not traveling to remote sites, resulting in fuel and energy savings.
Design for Deconstruction is a green building movement and resource mining tool that plans for a building’s dismantling from the design’s outset. Modular construction is uniquely suited to design for deconstruction because, as noted by Dru Meadows in Modular Building – A Green Lifecycle, “They are designed with attention to right-sizing and dematerializing components. They can be easily deconstructed and reused, repurposed or recycled.”
Repurposing buildings and materials for secondary locations is a natural consequence of both design for deconstruction and modular construction, and results in better energy usage. The Modular Building Institute indicates that “modular buildings can be disassembled and the modules relocated or refurbished for new use, reducing the demand for raw materials and minimizing the amount of energy expended to create a building to meet the new need.”
By nature, modular construction is greener: building offsite inevitably causes fewer site disturbances and environmental impacts because onsite traffic is significantly reduced, thus protecting green spaces and reducing carbon footprints. Another green advantage noted by the Modular Building Institute is that “modular structure[s] [are] completed in a factory controlled setting using dry materials, [so] the potential for high levels of moisture being trapped in the new construction is eliminated.”
Lastly, for project managers in Alberta, modular construction positively impacts construction schedules. Between eliminating weather delays and completing building construction off site in unison with site development, construction schedules are cut in half; quicker construction duration means less emissions and a speedy recovery for disturbed green spaces.
Wondering if your future construction project would be ideal for modular construction? Contact us for your free consultation!