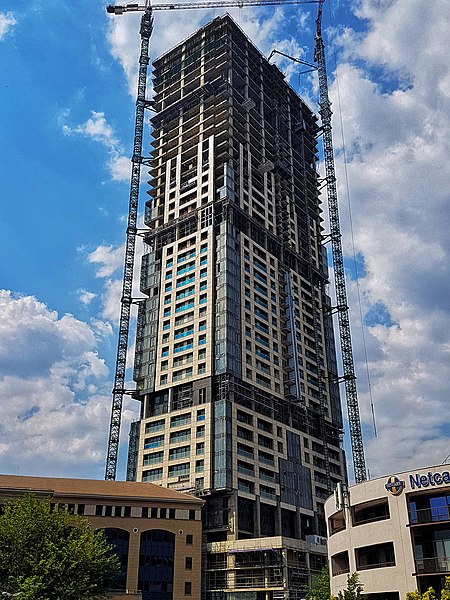
The hospitality industry has been at a setback since a few years because construction costs are on the rise. Since the damaging recession of 2008, the cost of workforce, raw material and managing costs for construction have been increasing. In such a downtrodden market, the hospitality industry is getting most of the burden as the base of their operations depends on construction. And when the construction costs go high, building a hotel before you can open it up to the public is demanding. And to top it all off, conventional construction is time-consuming, which means you have pressure from investors and partners if the work hangs at a point due to generic traditional construction issues.
Due to this hike in construction prices, there has to be an alternative to get away from the skyrocketing costs and still get to build for serving people. Modular construction can help in dodging the extreme costs of traditional construction for the hotel business. Here’s how.
How is Modular Construction Different than Traditional Construction?
To know how modular construction can help hospitality business, you must first understand how it is different from the traditional ways of construction that hotels have been using. Modular construction emerges from the same reason for which hotel industry can use it, the cost of conventional construction. After the end of the world wars, there was a somewhat similar issue with the construction industry. The charges were high, and the people still needed houses and healthcare centres. This is how the idea behind modular construction was born. Modular construction utilizes different raw materials for the development of a building in parts. It means that the buildings that were made under the modular construction method were not actually constructed but manufactured inside a factory. This is the most significant advantage of modular construction. The building to be built is designed like a set of Legos, i.e. it is manufactured in smaller parts inside a plant. While the manufacturing of the modules or components of a building is under progress, the foundation for the building is prepared. The prefabricated modules are then transported to the actual building site and are assembled together to form a complete structure. Modular construction very rarely uses the basic concrete assimilation for any of its construction process except preparing the foundation on which the modules are finally assembled.
Advantages of Modular Construction
Modular construction has many advantages over traditional construction including the cost efficiency.
Quality Control
In modular construction, 95% of the construction process goes on inside a factory. For the development of modules, there are no two different machines. The machines and materials are used for the construction of every ordered module. Still, the modules constructed are not necessarily the same. The same machines that are used for the manufacturing modules for a healthcare unit can be easily utilized in manufacturing customizable modules that can be placed on the foundation according to the clients’ demands. Every module built is constructed under the area’s building codes and regulations. The construction process can’t be harmed by any outdoor conditions because of the manufacturing inside the factory, so you don’t have to worry about the work being washed away by rain or concrete blown away with the wind.
Less Wastage
In traditional construction, the raw materials like gypsum and different kinds of steel are brought in with a rough calculation, considering wastage of material by labours or general wastage during construction. This material wastage is going to cost you because sometimes, when the raw materials go to waste, you have to add in extra to complete the job. Modular construction removes the wastage of materials by utilizing laser precision techniques. The assembly line method of manufacturing plant keeps track of all the material being used in the modules. Any unused material from the assembly line can be reused in the construction of the next module. This makes sure that the cost of construction remains under the budget specified by the client.
Less Construction Time
A very crucial factor in the hospitality business is time. Companies in the hospitality field are suckers for time and want to have their hotels constructed within record time because they too have pressure from their investors and plan partners. Modular construction can help clients with their deadlines. Modular construction process makes it easy to multitask in the manufacturing time. Firstly, 70-90% of the construction is done inside the factory. This prevents any weather conditions from slowing down the construction process or damaging structures already constructed. Secondly, while the construction process is on inside the factory, the preparations for the foundation can go on at the construction sites. This saves a lot of time for the owners and allows faster returns on their investments.
Customization
Modular construction has been using 3D printing technology to manufacture the parts for every building in an alternate manner. So when you opt for modular construction, the modules can be constructed using a design planned by the client themselves. Even when the construction is finished, the buildings can be altered later on if the need occurs. A different set of modules can be set upon existing modules according to the changed plans. This is a crucial need in the hotel industry as every hotel wants their building to look different than all the others in the area.
Since the increasing cost of construction has been giving the hospitality industry a hard time, it is highly recommended that modular construction should be used for the hotel buildings. The sustainability and eco-friendliness of modular construction make it a cost-efficient alternative for the hospitality sector. For queries on modular construction or a quote on construction costs, get in touch with Cormode & Dickson.