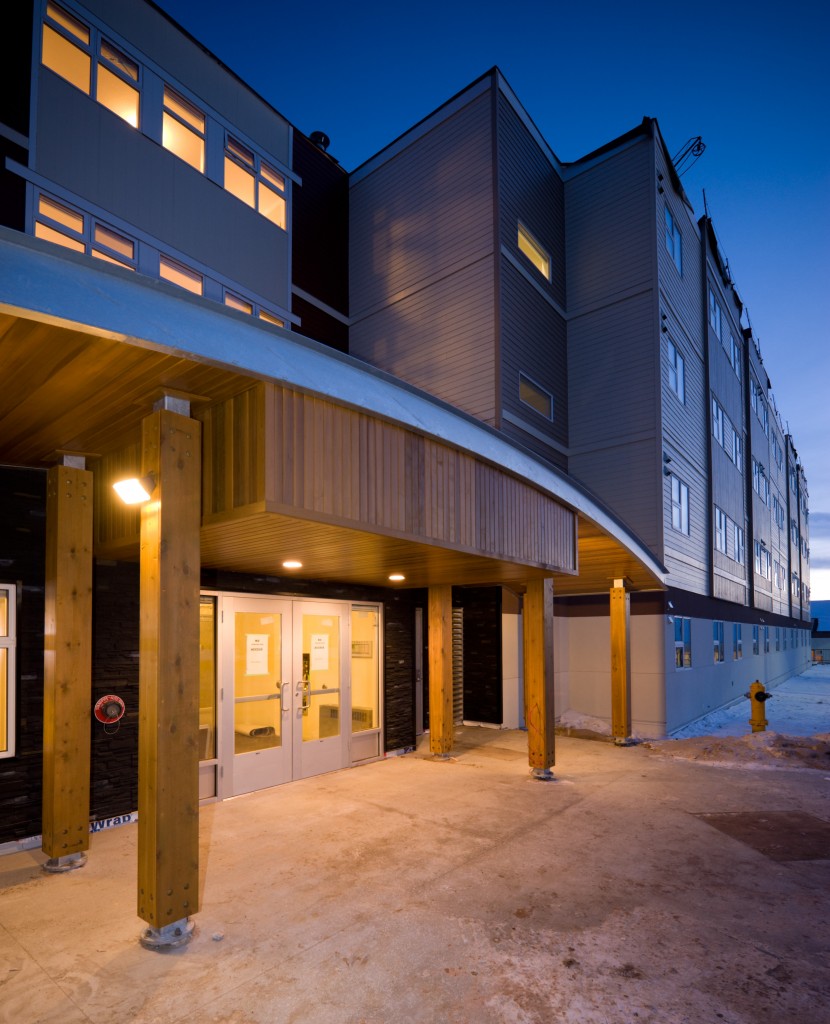
Modular construction, from the hospitality industry, retail petroleum, apartment complexes, to work camps, is a growing trend in both the Canadian and North American construction industry. With advances in technology, modular construction has vastly improved over the years, and what was once a niche market service, has become a force to be reckoned with in today’s market, equal to or better than conventional construction in many ways.
James Flake, director of operations with Jacobs, “Just eight to ten years ago, we were one of only a few engineering, procurement and construction (EPC) firms bringing modular construction into the discussion. Now, our clients are modular-savvy and ask us to talk about them. We have a client who says their philosophy used to be, ‘Help me understand why we should use modules,’ but now jokes and says our job is to help them understand where they shouldn’t use modules.”
But should your next project be built modular? Here’s some reasons why modular may be the best way to go.
One of the greatest advantages of modular is its expedited schedule. Modular construction will cut the building schedule of a project by at least 6 to 12 weeks, when compared to conventional construction. That means 6 to 12 weeks or more of increased revenue for your construction project and 6 to 12 weeks of labour cost savings.
When you build in a weather-controlled factory, there are less complications due to rain, wind, snow, or other volatile weather conditions, which could compromise materials, leading to a higher level of quality control. Depending on the location of your proposed sites, you won’t have to shut down major arterial road ways or obstruct traffic for long periods of time. Building in an off-site factory allows for parallel building. You can have the modules on-site and ready right as the foundation has been completed and the concrete has cured. With everything pre-planned and with less outside complications, there is much greater schedule certainty with modular construction.
Another defining characteristic of modular is its resource efficiency and green technology. Not only is the build more energy efficient with less material waste, almost all of today’s modular buildings are constructed with energy efficiency in mind. In today’s modular world, almost all modular buildings are made up of recycled metal, recycled glass, and recycled wood. But beyond recycled materials, the individual modules themselves can be recycled. Building demolitions and material waste are a thing of the past. With modular, it’s on to a brighter and greener future.
Simply put, all this amounts to are cost savings for our clients. According to a report by the Building Industry Association of Philadelphia, going modular can reduce construction costs to 9-20% on home-building.
So, if there are cost savings, greener technology, safety improvements, material improvements, schedule advantages, and less complications, the question “should I build my project modular?” seems to have a clear answer. According to the Modular Building Institute (MBI), modular construction, with its numerous advantageous over conventional construction, has been labelled the “future of construction” and we couldn’t agree more.
Download the ESSENTIAL 5 point checklist: Is Modular Right For Your Project?